Методы испытаний
- Методы испытаний при входном контроле качества сырья и материалов указывают в технологической документации на изготовление изделий с учетом требований нормативных документов на это сырье и материалы.
- Методы испытаний при проведении производственного операционного контроля устанавливают в технологической документации на изготовление изделий.
- Размеры изделий, толщину наружных стенок, диаметр цилиндрических пустот, размеры квадратных и ширину щелевидных пустот, длину посечек, площадь отколов и длину отбитостей ребер изделий измеряют металлической линейкой по ГОСТ 427 или штангенглубиномером по ГОСТ 162. Погрешность измерения — ± 1 мм.
3.1 Длину и ширину каждого изделия измеряют в трех местах изделия: на двух ребрах и середине
постели, толщину — на двух ребрах и середине тычка.
За результат измерений принимают среднеарифметическое значение результатов единичных измерений.
3.2 Ширину раскрытия трещин измеряют при помощи измерительной лупы по ГОСТ 25706, после чего изделие проверяют на соответствие требованиям 5.2.4. Погрешность измерения — ± 0,1 мм
3.3 Глубину отбитости углов и ребер измеряют при помощи штангенглубиномера по ГОСТ 162 или угольника по ГОСТ 3749 и линейки по ГОСТ 427 по перпендикуляру от вершины угла или ребра, образованного угольником, до поврежденной поверхности. Погрешность измерения — ± 1 мм.
- Отклонение от перпендикулярности граней определяют, прикладывая угольник к смежным граням
изделия и измеряя металлической линейкой наибольший зазор между угольником и гранью. Погрешность
измерения — ± 1 мм.
За результат измерений принимают наибольший из всех полученных результатов.
- Отклонение от плоскостности изделия определяют, прикладывая одну сторону металлического угольника к ребру изделия, а другую — вдоль каждой диагонали грани и измеряя щупом по действующему нормативному документу или линейкой по ГОСТ 427 наибольший зазор между поверхностью и ребром угольника. Погрешность измерения — ± 1 мм.
За результат измерения принимают наибольший из всех полученных результатов.
- Наличие известковых включений определяют после пропаривания изделий в сосуде.
Образцы, не подвергавшиеся ранее воздействию влаги, укладывают на решетку, помещенную в сосуд с крышкой. Налитую под решетку воду нагревают до кипения. Кипячение продолжают в течение 1 ч. Затем образцы охлаждают в закрытом сосуде в течение 4 ч, после чего их проверяют на соответствие требованиям 5.2.2.
- Для определения наличия высолов половинку изделия погружают отбитым торцом в сосуд, заполненный дистиллированной водой, на глубину 1—2 см и выдерживают в течение 7 сут (уровень воды в сосуде должен оставаться постоянным). По истечении 7 сут образцы высушивают в сушильном шкафу при температуре 100 "С до постоянной массы, а затем сравнивают со второй половинкой образца, не подвергавшейся испытанию, проверяя на соответствие 5.2.3.
- Предел прочности при сжатии кирпича и камня и кирпича при изгибе определяют в соответствии с ГОСТ 8462.
Предел прочности при сжатии крупноформатного камня определяют на целом изделии. Выравнива¬ние опорных поверхностей камня производят шлифованием и применением пластины из технического войлока или из конвейерных резинотканевых лент.
Образец крупноформатного камня устанавливают в центре испытательной машины и прижимают верх¬ней плитой машины. При испытаниях нагрузка на образец должна возрастать непрерывно и равномерно со скоростью 5—10 кН/с. Предел прочности при сжатии Rсж, МПа (кгс/см2), вычисляют по формуле
где Р — максимальная нагрузка, при которой разрушается образец, МН (кгс);
F — среднеарифметическое значение площадей верхней и нижней граней образца, м2 (см2). Предел прочности при сжатии образцов вычисляют с точностью до 0,1 МПа (1 кгс/см2) результатов испытания всех образцов
- Среднюю плотность, водопоглощение и морозостойкость (метод объемного замораживания) из-
делий определяют в соответствии с ГОСТ 7025.
Отклонение каждого значения средней плотности допускается не более:
для классов 0,8 и 1,0 — + 50 кг/м3;
для остальных классов — + 100 кг/м3.
Водопоглощение определяют при насыщении образцов водой температурой (20 ± 5) °С при атмосферном давлении.
Морозостойкость определяют методом объемного замораживания.
- Удельную эффективную активность естественных радионуклидов AЭФФ определяют по ГОСТ 30108.
- Коэффициент теплопроводности кладок определяют по ГОСТ 26254 со следующими дополне-
ниями.
Коэффициент теплопроводности определяют экспериментально на фрагменте кладки, которую с уче¬том растворных швов выполняют толщиной из одного тычкового и одного ложкового рядов кирпичей или камней. Кладку из укрупненных камней выполняют в один камень. Длина и высота кладки должны быть не менее 1 ,5 м (см. рисунок 1 ). Кладку выполняют на сложном растворе марки 50, средней плотностью 1800 кг/м
3, состава 1,0:0,9:8,0 (цемент:известь:песок) по объему, на портландцементе марки 400, с осад¬кой конуса для полнотелых изделий 12 — 13 см, для пустотелых — 9 см. Допускается выполнение фрагмента кладки, отличной от указанной выше, с применением других растворов, состав которых указывают в протоколе испытаний.
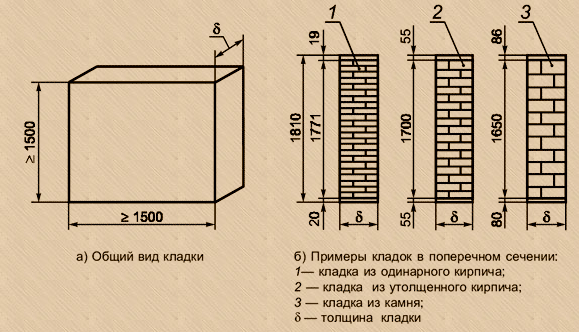
Рисунок 2 — Фрагмент кладки для определения теплопроводности
Фрагмент кладки из изделий со сквозными пустотами следует выполнять по технологии, исключающей заполнение пустот кладочным раствором или с заполнением пустот раствором, о чем делается запись в протоколе испытаний. Кладку выполняют в проеме климатической камеры с устройством по контуру теплоизоляции из плитного утеплителя; термическое сопротивление теплоизоляции должно быть не менее 1,0 м2·°С/Вт. После изготовления фрагмента кладки его наружную и внутреннюю поверхности затирают штукатурным раствором толщиной не более 5 мм и плотностью, соответствующей плотности испытуемых изделий, но не более 1400 и не менее 800 кг/м3.
Фрагмент кладки испытывают в два этапа:
- этап 1 — кладку выдерживают и подсушивают в течение не менее двух недель до влажности не более 6%;
- этап 2 — проводят дополнительную сушку кладки до влажности 1% — 3%.
Влажность изделий в кладке определяют приборами неразрушающего контроля. Испытания в камере проводят при перепаде температур между внутренней и наружной поверхностями кладки Δt=(tB-tH)≥40°C температуре в теплой зоне камеры tв=18°С—20°С, относительной влажности
воздуха (40 ± 5) %. Допускается сокращение времени выдержки кладки при условии обдува наружной поверхности и обогрева внутренней поверхности фрагмента трубчатыми электронагревателями (ТЭНами), софитами и др. до температуры 35 °C — 40 °С.
Перед испытанием на наружной и внутренней поверхностях кладки в центральной зоне устанавливают не менее пяти термопар по действующему нормативному документу. Дополнительно на внутренней поверхности кладки устанавливают тепломеры по действующему нормативному документу. Термопары и тепломеры устанавливают так, чтобы они охватывали зоны поверхности ложкового и тычкового рядов кладки, а также горизонтального и вертикального растворных швов. Теплотехнические параметры фиксируют после наступления стационарного теплового состояния кладки не ранее чем через 72 ч после включения климатической камеры. Измерение параметров проводят не менее трех раз с интервалом в 2 - 3 ч.
Для каждого тепломера и термопары определяют среднеарифметическое значение показаний за период наблюдений qi и ti . По результатам испытаний вычисляют средневзвешенные значения температуры наружной и внутренней поверхностей кладки
с учетом площади ложкового и тычкового измеряемых участков, а также вертикального и горизонтального участков растворных швов по формуле
(1)
где ti — температура поверхности в точке i, °С
Fi — площадь i-го участка, м2
По результатам испытаний определяют термическое сопротивление кладки
с учетом фактической влажности во время испытаний по формуле
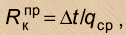
(2)
где 
qcp— среднее значение плотности теплового потока через испытываемый фрагмент кладки, Вт/м2
По значению
вычисляют эквивалентный коэффициент теплопроводности кладки λЭКВ(ω), Вт
/(м·°C) по формуле
(3)
где δ — толщина кладки, м.
Строят график зависимости эквивалентного коэффициента теплопроводности от влажности кладки λЭКВ Вт/(м·°С), по формуле
(4)
Коэффициент теплопроводности кладки в сухом состоянии λ0 Вт/(м·°С) вычисляют по формуле
или (5)
(6)
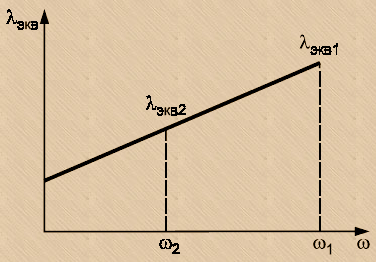
Рисунок 3 — График зависимости эквивалентного коэффициента теплопроводности от влажности кладки
За результат испытания принимают среднеарифметическое значение коэффициента теплопроводности кладки в сухом состоянии λ0, Вт
/(м·°C)вычисленное по формуле
(7)